TRANSEC - Moisture monitoring & drying
The issue: Moisture is threatening the transformer
Moisture is one of the primary causes of failures for power transformers and one of the main degradation factors for the insulation paper. It, therefore, increases the risks of operation failures and shortens the life expectancy of the asset.
Unfortunately, moisture can appear in a transformer from several sources, which are external or internal and it has a complex dynamic between the oil and paper within the transformer. The use of silica gel breathers, sealed tanks or nitrogen blankets can avoid all or at least the most of moisture from the atmosphere to affect the transformer. However, when the transformer is energised, the production of water inside the insulation is a natural and inevitable occurrence over time due to the depolymerisation of the cellulose paper.
Only continuous filtration is efficient in removing moisture from a transformer
As moisture is created continuously and as it is one of the primary concern for the transformer safety and life expectancy, it seems counter-intuitive to apply a temporary solution for this ongoing problem. Also it is essential to note that more than 98% of the water in a transformer is in the paper, while a meagre amount is dissolved in oil. The diffusion time of water from paper to oil is prolonged. This is why punctual filtrations are not solving the moisture issue.
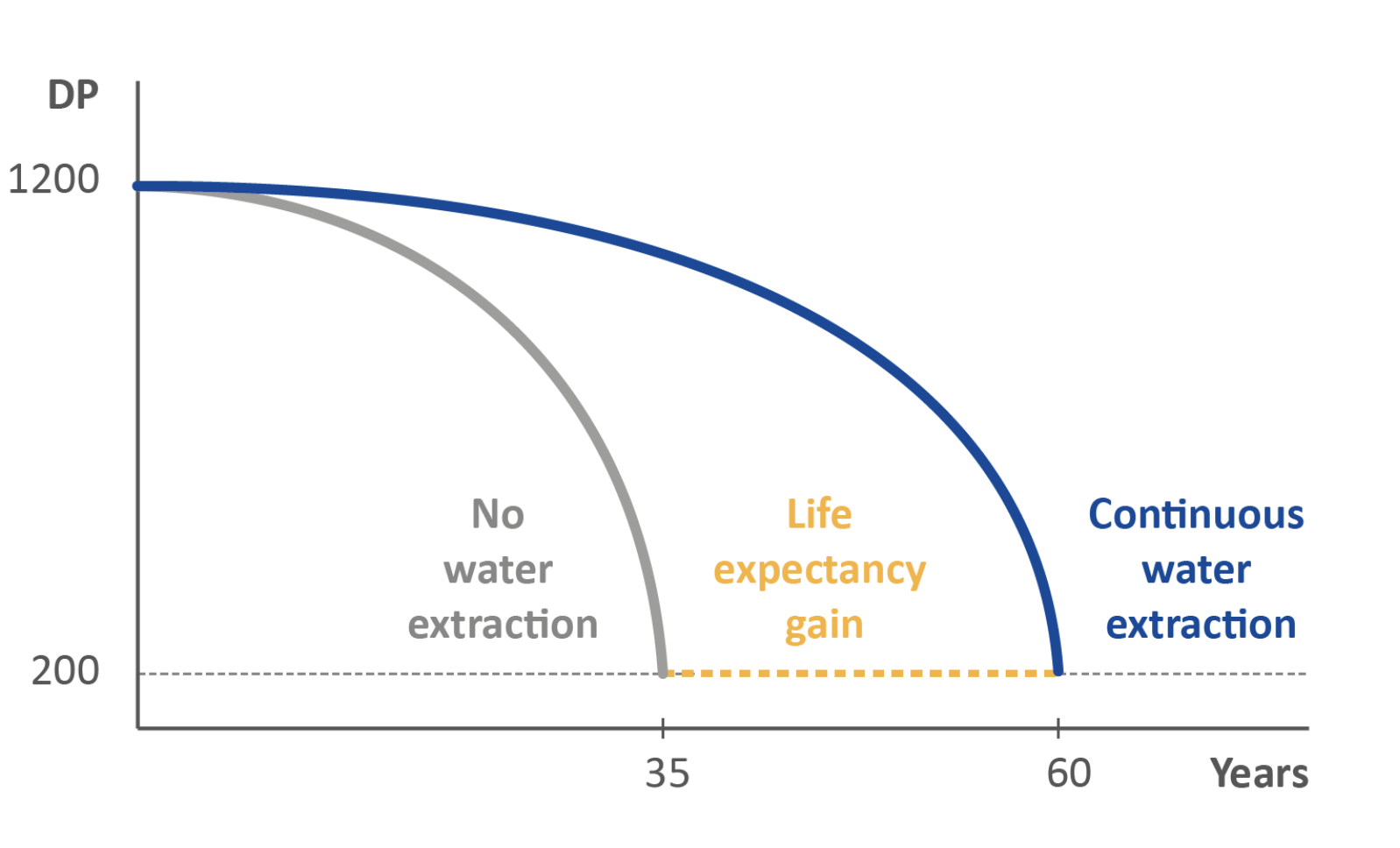
The issue: Assessing the amount of water in the transformer
- More than 98% of the water present in the transformer is contained in the paper insulation while less than 2% is in the oil. Unfortunately, the insulation paper is not easily accessible for water assessment.
- Water solubility in oil varies depending on oil temperature and therefore PPM differs also. Hence it is not possible to check the PPM value to define the amount of water in paper.
- If PPM and oil temperature are known some curves to link the water PPM in oil and the water content in the paper. But these curves are only really valid at equilibrium which is in general never reached on a running transformer.
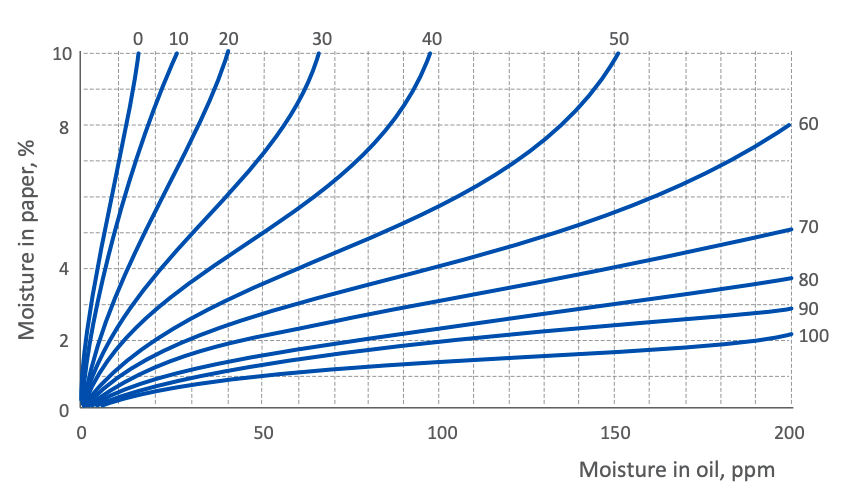
- As the water diffusion time is faster from the paper to the oil than the opposite it is possible to reach on the same transformer, several very different PPM values for the same oil temperature even at a few days difference.
- As a result of the previous points, taking an oil sample once or twice per year to assess the moisture level in the transformer seems irrelevant.
- Furthermore, oil samples can be contaminated at the sampling time or in the laboratory. As the moisture level is anyway very low in oil, any contamination (simple contact with the ambient air) will affect the sample PPM result. The chart shows PPM analysis results of 7 different laboratories on 3 different oils.
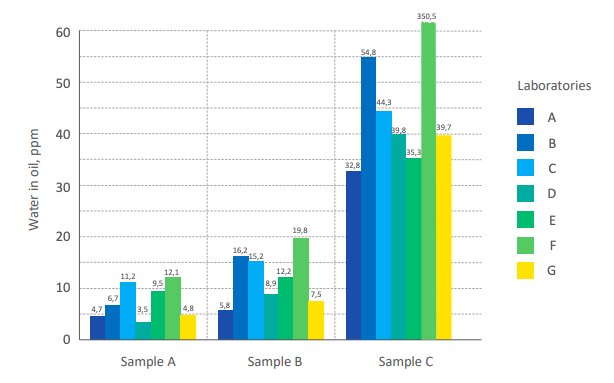
The solution: TRANSEC online drying system
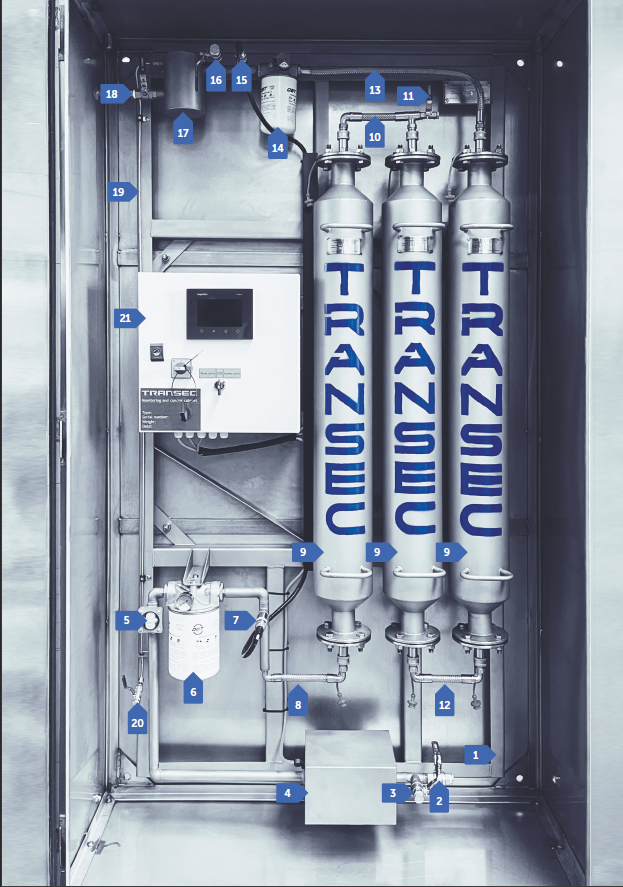
- 1. Frame
- 2. Inlet ball valve
- 3. Inlet sampling valve
- 4. Pump
- 5. Flow indicator
- 6. Inlet filter
- 7. Inlet moisture and temperature sensor
- 8. Bottom interconnection pipeline between cylinder and sensor/inlet filter
- 9. Cylinders
- 10. Top interconnection pipeline between cylinders
- 11. Air bleed valve between cylinders
- 12. Bottom interconnection pipeline between cylinders
- 13. Top interconnection pipeline between cylinder and outlet filter
- 14. Outlet filter
- 15. Outlet moisture and temperature sensor
- 16. Outlet sampling valve
- 17. Deaerator
- 18. Outlet ball valve
- 19. Bleed pipe
- 20. Deaerator air bleed valve
- 21. AMi monitoring and control cabinet (MCC)
The solution: TRANSEC online drying system CL4 iVersion
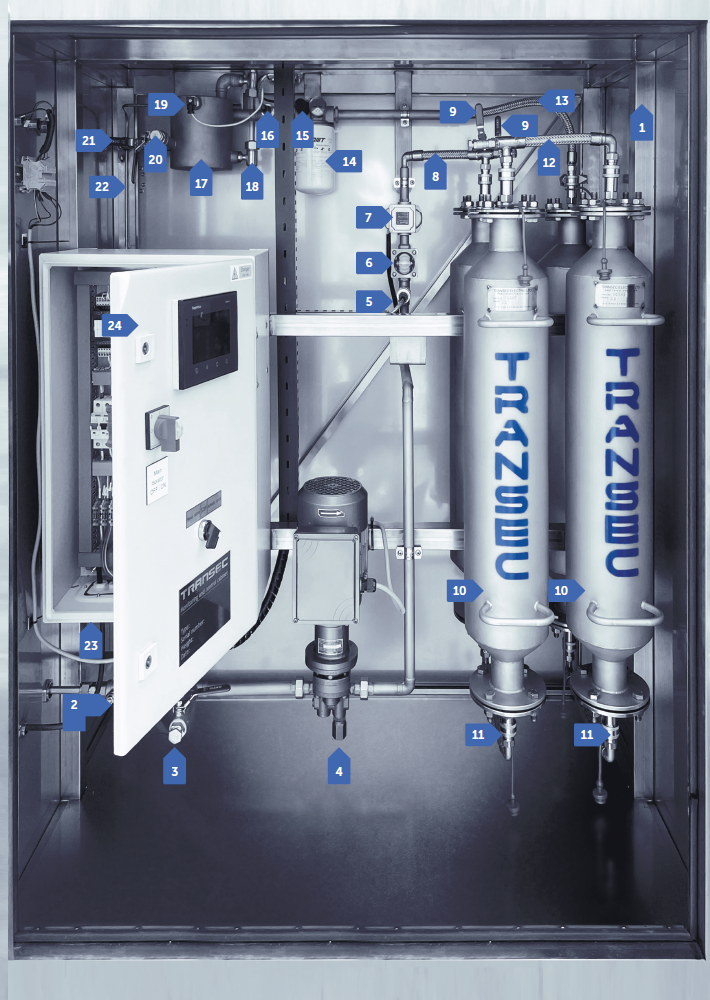
- 1. External enclosure
- 2. Inlet ball valve
- 3. Inlet sampling valve
- 4. Pump
- 5. Inlet moisture and temperature sensor
- 6. Flow indicator
- 7. Flow meter
- 8. Top interconnection pipeline between cylinder and sensor
- 9. Air bleed valve on the first cylinder and air bleed valve between second and third cylinders
- 10. Cylinders
- 11. Bottom interconnection pipelines between cylinders
- 12. Top interconnection pipeline between cylinders
- 13. Top interconnection pipeline between cylinder and outlet filter
- 14. Outlet filter
- 15. Particle filter sensor
- 16. Outlet moisture and temperature sensor
- 17. Deaerator
- 18. Glass gauge
- 19. Float switch
- 20. Outlet sampling valve
- 21. Outlet ball valve
- 22. Bleed pipe
- 23. Deaerator air bleed valve
- 24. WSi monitoring and control cabinet (MCC)
TRANSEC Online Drying System uses molecular sieves to extract moisture from the oil. These granules (non-chemical) contain many pores of 3 angstrom diameter which is the exact size to catch water molecules. That way other components like gases molecules with larger or smaller diameter are not filtered by these sieves.